Comprehending the Basics and Applications of Plastic Extrusion in Modern Production
In the realm of modern production, the method of plastic extrusion plays a critical function - plastic extrusion. This complex process, entailing the melting and shaping of plastic via specialized dies, is leveraged across different markets for the creation of varied products. From car parts to durable goods packaging, the applications are vast, and the potential for sustainability is equally remarkable. Deciphering the fundamentals of this procedure exposes truth convenience and capacity of plastic extrusion.
The Basics of Plastic Extrusion Process
While it might appear complex, the basics of the plastic extrusion procedure are based on fairly uncomplicated concepts. It is a manufacturing process in which plastic is thawed and then shaped into a continual profile via a die. The plastic extrusion procedure is extensively utilized in different industries due to its efficiency, cost-effectiveness, and versatility.
Different Sorts Of Plastic Extrusion Techniques
Building upon the fundamental understanding of the plastic extrusion procedure, it is necessary to discover the different techniques included in this production approach. In comparison, sheet extrusion develops huge, level sheets of plastic, which are commonly further refined right into items such as food packaging, shower curtains, and auto components. Understanding these methods is essential to utilizing plastic extrusion effectively in contemporary manufacturing.
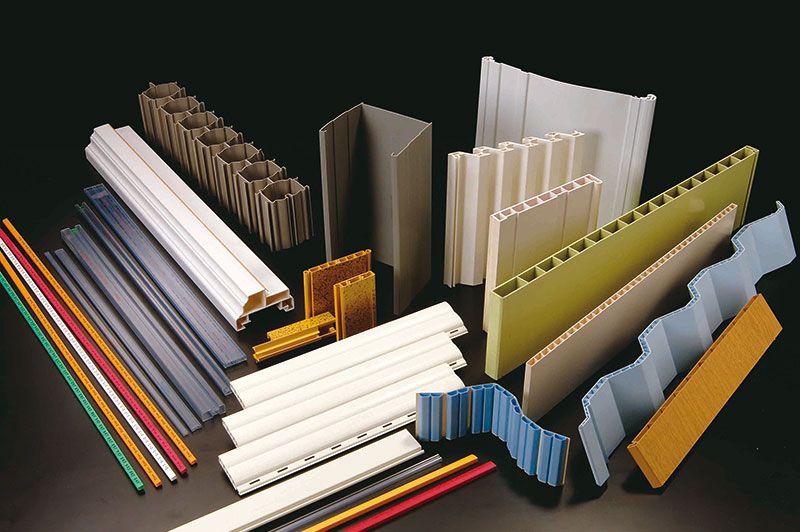
The Function of Plastic Extrusion in the Automotive Market
A frustrating bulk of components in contemporary cars are products of the plastic extrusion procedure. This procedure has transformed the vehicle industry, transforming it into a much more efficient, cost-effective, and adaptable production industry. Plastic extrusion is mainly made use of in the manufacturing of numerous auto components such as bumpers, grills, door panels, and dashboard trim. The process gives an uniform, regular outcome, making it possible for manufacturers to generate high-volume get rid of excellent accuracy and minimal waste. The lightness of the extruded plastic components adds to the overall decrease in lorry weight, boosting fuel performance. The sturdiness and resistance about his of these components to heat, cold, and effect boost the longevity of vehicles. Therefore, plastic extrusion plays a crucial role in vehicle production.
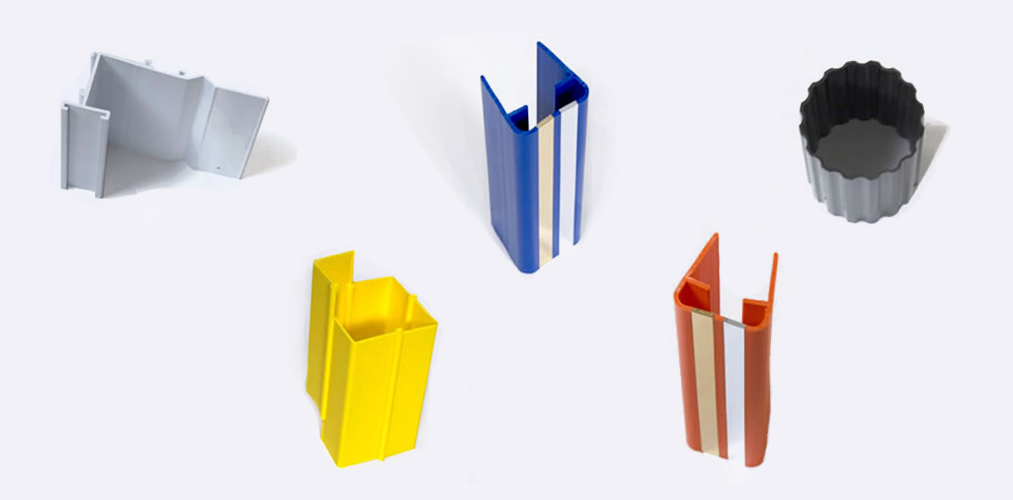
Applications of Plastic Extrusion in Durable Goods Manufacturing
Past its significant effect on the auto industry, plastic extrusion verifies just as effective in the world of customer goods producing. The convenience of plastic extrusion allows producers to make and produce complicated forms and dimensions with high accuracy and performance. The flexibility, adaptability, and cost-effectiveness of plastic extrusion make it a favored selection for several consumer goods makers, adding significantly to the industry's growth and advancement.
Environmental Influence and Sustainability in Plastic Extrusion
The prevalent use of plastic extrusion in making welcomes scrutiny of its environmental implications. As a process that regularly makes use of non-biodegradable products, the ecological influence can be substantial. Power intake, waste manufacturing, and carbon exhausts are all problems. Sector innovations are raising sustainability. Reliable equipment minimizes power usage, while useful source waste monitoring systems reuse scrap plastic, reducing basic material demands. Additionally, the growth of eco-friendly plastics supplies a much more eco-friendly choice. Regardless of these renovations, even more innovation is required to minimize the environmental footprint of plastic extrusion. As culture leans in the direction of sustainability, makers should adapt to continue to be feasible, emphasizing the importance of continual study and innovation in this field.
Final thought
In verdict, plastic extrusion plays a vital function in contemporary production, specifically in the auto and customer items sectors. Comprehending the fundamentals of this process is vital to optimizing its benefits and applications.

The plastic extrusion procedure is extensively made use of in numerous markets due to its flexibility, cost-effectiveness, and efficiency.
Structure upon the fundamental understanding of the plastic extrusion process, it is needed to explore the numerous methods involved in this manufacturing approach. plastic useful source extrusion. In contrast, sheet extrusion develops huge, flat sheets of plastic, which are usually further refined into items such as food packaging, shower drapes, and vehicle components.An overwhelming bulk of parts in modern-day vehicles are items of the plastic extrusion process